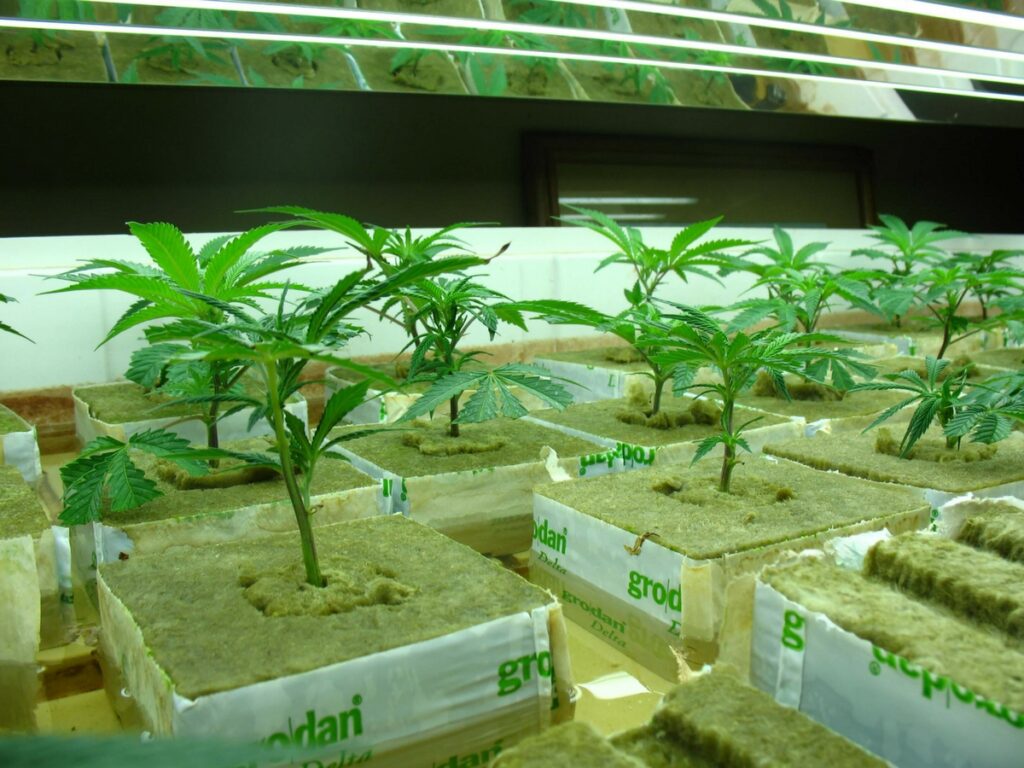
Influencing air quality
The amount of CO2 in the open air is approximately 0.03 to 0,04%. The amount of carbon dioxide is also expressed in parts per million; ppm. 0.03% is equal to 300 ppm. There are differences in the CO2 needs among plants. By raising the CO2 content, growth can be accelerated. The law of diminished returns still holds true, however. Raising the CO2 level has limits, but at approximately 1400 ppm (0.14%), good results (a faster growth) are generally achieved. Above 1400 ppm, the effect of a higher percentage of CO2 decreases. A high concentration of CO2 is poisonous even for plants. A CO2 concentration of 1800 ppm or more is deadly for most plants. A simple method for guaranteeing the supply of carbon dioxide is to ventilate the room. Sufficient ventilation must be provided, so the plants keep getting enough fresh CO2. A second and just as important reason for ventilation, is to dispose of excess heat. If the temperature gets too high, (see Section 5.4), growth is stunted. This counts not only for the temperature in the grow room, but also for the temperature in the plant itself. When the plant’s temperature is too high (humans get a fever), there is less sap flow, causing growth disturbances. There is no standard solution for refreshing the air. The need for fresh air is, for a large part, dependent on the size of the grow room in cubic meters. In principal, the total air content of the room must be exchanged every 2-3 minutes. Using for example a grow room 3 meters long, 2 meters wide, and 2 meters high (12m3), this means that the ventilator capacity must amount to 30 x 12 = 360 m3 per hour. A standard bathroom ventilator can only handle up to 100 m3 per hour Many growers ventilate their rooms with table fans. The point is the control of the temperature as well as the circulation of the air with sufficient carbon dioxide. Table fans are primarily intended to keep people comfortable on a hot summer day. They are much less suited to run continually for heat removal, and for CO2-content maintenance. Table fans have a tendency to melt with intensive use. You can imagine the consequences: not only the danger of fire, but also massive plant death . . . There are, of course, plenty of fans on the market which will take care of proper ventilation. These have been specifically designed to be able to run continually. The CO2 content in the grow room can also be heightened by adding CO2 from a tank. If the system is set with a timer clock, the desired amount of CO2 can be regularly released. Work with care, because you don’t know how much CO2 is in the room at any given moment. An overdose can easily occur To prevent this, it’s sensible to ventilate the area well before each CO2 ‘injection’. The most professional option is to use a CO2 controller. This apparatus continually measures the CO2 content in the room. When the programmed minimum value is reached, CO2 is automatically added. If the programmed maximum is exceeded, the controller turns on the ventilating system. If CO2 is added to the room via a tank, or a controller, cultivation can take place at a higher temperature. (More about this aspect in Section 5.4.) Ultimately, attention must be given to the relationship between ventilation, and the relative air humidity. The humidity of the air is dependent, among other things, on the amount of air moved through the room. Changing the air draws more moisture out of the plants, because the stomata release more moisture. If the relative humidity of the air drops too low, the stomata close, delaying the growth process.